開発の目的と経過
|
鋳物工場に於いて生産される各種鋳造品は、鋳ばなし後、素形材製品として一次・二次加工工場へ供給する場合、一般に鋳物生産工場内で二次行程として、何等かの手段で、押し湯・堰・湯道、あるいは鋳型組み込み時に発生する鋳ばり等を除去しなければなりません。これを、鋳仕上げ作業と称しておりますが、この鋳仕上げ作業は、砥石を使用するので多量の粉塵と騒音および悪臭を発生させ、そのため作業者は防塵・防音装備で作業となり、非常にきつい労働で、人材確保が難しくなっております。
このような現況の中、業界においては改善が叫ばれてはおりますが、進行状況は捗々しくありません。一部、自動機などが導入され機械化されている部門もありますが、鋳造品の形状が多岐に渡る事や寸法精度がネックとなって大半は手作業に頼らざるを得ない状況です。
そこで、ダイヤモンド工具が適用できればこのような状況を改善出来るのではないかと考え、数年前にその開発を決定致しました。
ダイヤモンドによる金属材料の加工は非常に範囲が狭く、とりわけ、金属切断加工には不適合とされていました。
セラミックス(一般に難切削材)の切断にダイヤモンド切断砥石が多用されていますが、鋳鉄ボンドを用いたものが優れた特性を呈するとの情報より、切削時に黒鉛が有効に作用するなら鋳物の切断が可能ではないかと考え、鋳物工場の動向を調査し、研究と現場試験を重ねることにより、FCおよびFCDに適用するダイヤモンド工具の開発に成功致しました。
|
1.現行の鋳仕上げ作業
|
鋳造方式によって異なるが、大略以下のような手段がとられています。
1.1 押し湯・堰など余分な部分の除去作業
1)電動工具などに砥石を取付け切断する。
2)パッカーなどの、手持式機械にて破断する。
3)単純なハンマーリング(ハンマーによる打撃)や、サイシング(フォーミング
などによる破談。
4)ガスバーナー溶断機等による溶断。
上記方法が採用できない大型鋳物、鋳鋼関係で多く適用されています。
1.2 鋳ばりや鋳肌荒れ部分、および上記処理後の表面仕上げ作業
1)電動工具などに砥石を取付け研削する。
(手持ち式、フロアスタンドグラインダー)
2)特殊なプレス機械で除去。
3)専用装置での自動処理(比較的生産量の多いもの)
|
2.現行作業の問題点
|
2.1 砥石による切断・研削
1)一般的に使用されている砥石は所謂レジノイド砥石(砥粒をフェノール樹脂で
結合したもの)であって、粉塵と悪臭の発生が避けられず、そのため、作業
環境が悪く、安全衛生上にも問題があります。
2)又、レジノイド砥石の寿命は短く工具の交換が頻繁です。
3)切断作業において、ワークによっては、砥石外径が20〜30%摩耗すると使用
できない例もあり有効に利用できません。
2.2 パッカーやハンマーリングによる破断
1)身喰い不良が生じる
2)仕上がり状態のばらつきが大きく、次の研削作業が増えます。
2.3 溶断法
1)機械切断に比べ処理時間が早いが、その後の粗研工数が増加します。
2)切断面近傍の材質に変化を与えます。
|
▲このページの先頭へ戻る
|
ダイヤモンド工具の特徴
|
1.開発した銑鉄鋳物用ダイヤモンド工具のメリット
|
1)ライフが長く、そのため工具交換に費やされる時間が短縮できます。
ライフは使用条件に左右されますが、現行のレイジノイド砥石の数十倍から
百倍以上を期待できます。
2)切れ味、研削性が良く加工面がきれいです(用途による)。
3)その結果、手作業の場合は作業者への負担が軽くなり、かつエネルギー
(燃費、消耗電力)が低下します。
4)また、発熱が減少しそのため、処理物の組織変化を生じさせ難い。
5)工具の摩耗は極僅かなので外径の現象による使用不可、という現象は
生じません。また、自動機では摩耗によるテーチィングのやり直しを実地する
必要がなく、摩耗測定装置・制御機器を省くことが出来、安価となります。
6)発生する粉塵は処理物によるものだけであるので、量が半減します。
そのため、作業環境が改善され、また集塵機を小型にでき経費節減
となります。
7)レジノイド砥石のように悪臭は発生しません。
8)特に、切断ブレードの場合は基盤が特殊な鋼材を採用していますので、破損
などの事故は通常の状態では発生しません。また、ダイヤ部分はろう付
タイプでありませんのでチッブの破損等は生ぜず、極めて安全です。
9)製品を構成する材料は鋼材とダイヤモンド(カーボン)、微小のCu、Niだけ
ですので、使用済み品を廃棄する場合鉄屑として処分出来ます。
|
2.開発したダイヤモンド工具の問題点
|
1)残念ながらオールラウンドではありません。現行、適用できる材質は
FCおよびFCD、一部銅合金に限られます。
2)価格が従来の砥石に比べると高価であるので、条件が不適当であったり、
作業ミス等で損傷(基盤の変形、ダイヤの破損・焼き付け)を早期に
引き起こした場合は、高い買い物となってしまします。
3)自動機等に使用した場合、テーチングのミス等で砥石をワークにぶつけ
てしまった際は、従来の砥石は砥石自身が破損しショックを吸収し装置
本体に損傷を与える事が少ないのですが、開発した砥石の場合は基盤が
鋼であり強度があるので装置に損傷を与える恐れがあります。
4)特に不適当な条件
■一回当たりの加工面が著しく広い場合放熱が悪いためで、
エアで強制的に冷却すれば使用できる
■負荷が過大(時間当たりの研削量が多い場合)
■使用する装置の不具合
芯振れが大きい、剛性が小さい、ワークの保持が甘い、砥石周速が遅い
|
▲このページの先頭へ戻る
|
ダイヤブレード・アクアブレードの使用限界の見極め
|
アクアブレードは基板表面にダイヤモンド粒が一粒ずつ一層、メッキで包み込まれて付着させられているもので、ダイヤが1層摩耗すれば寿命となります。
使用するにつれ、ダイヤ粒のエッヂは摩耗し徐々に切れ味が低下してきますが、寿命に近づいてきますと切れ味が急激に低下します。
この時ブレード外周部を観察すると、通常基板が発熱により紫色状に変色し、さらによく観察すると基板外周部にヘアクラックが生じてきています。
|
この状態になったら使用は出来ません ! !
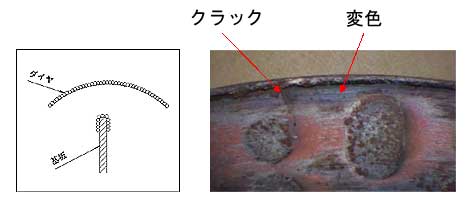
|
このまま続行しますと、急激にクラックが進行しブレードの破損につながり、重大事故を招く結果になるやもしれませんので、必ず新しいものに取り替えて下さい。
|
■仕様前の点検事項
|
(1) ブレード概観の観察
|
■ 基板の変形の有無
|
■ クラック発生の有無
|
■ 基板変色の有無
|
■ ダイヤ損耗状況
|
(2) エンジンカッタに取り付けて−
|
■ 手で空回しをカバーとの間隔、基板振れの確認
|
■ 空運転し、基板振れ、異常な振動等の有無の確認
|
※ なお、製品ケースに印刷された説明文もお読み下さい ※
|
|
▲このページの先頭へ戻る
|